Materialkunde GfK/CfK – Teil 1: Basiswissen und Herstellung von Heli-Anbauteilen
Faserverbundwerkstoffe sind aufgrund ihrer vielseitigen Eigenschaften aus dem Modellhelikopterbau
nicht mehr wegzudenken. So kommen kohlefaserverstärkte Kunststoffe am Chassis und bei Rotorblättern zum Einsatz, wohingegen Fiberglas in erster Linie für Rümpfe und Hauben verwendet wird. Dr. Klaus Huber erklärt in einer mehrteiligen Artikelserie, worin sich die Materialien unterscheiden und wie sich beispielsweise CfK für Kufenbügel und Co. verarbeiten lässt.
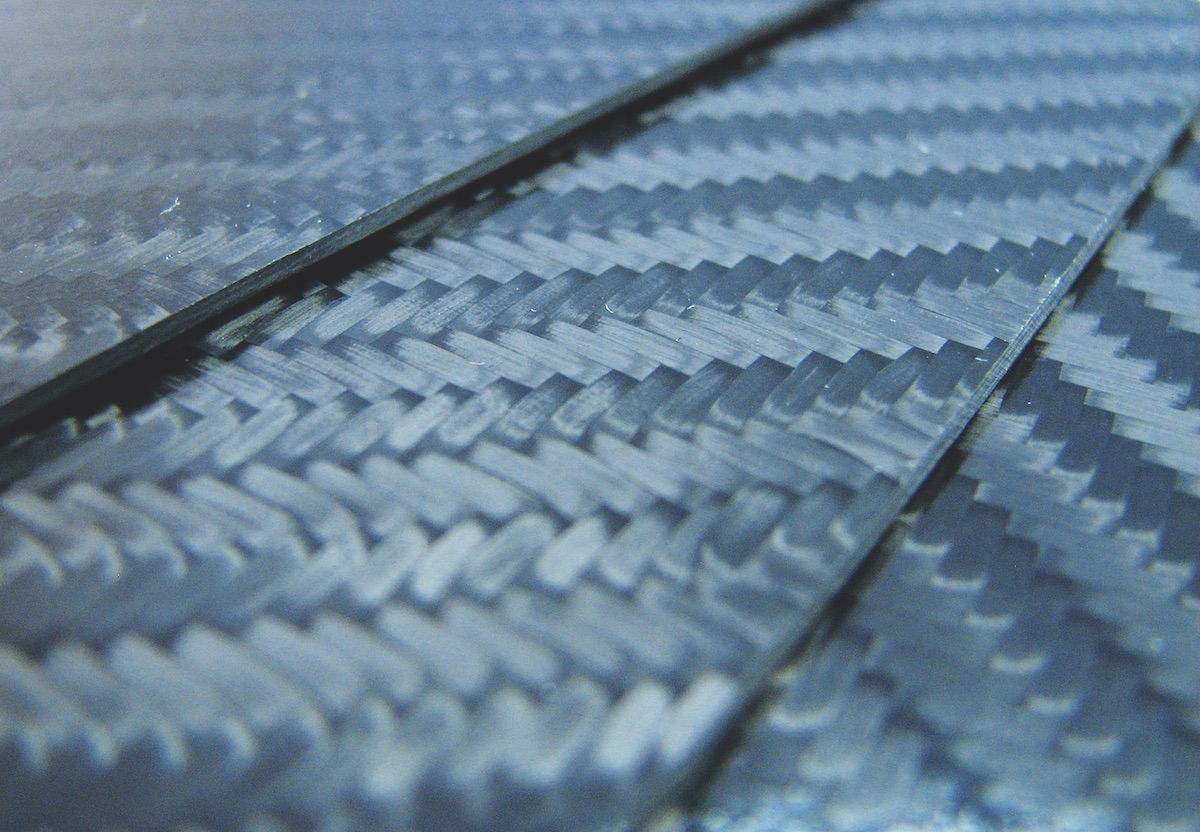
GfK wird umgangssprachlich auch Fiberglas genannt. Dieser Begriff stammt aus dem Englischen, da das Wort Glasfaser mit »glass fibre« übersetzt wird (glasfaserverstärkter Kunststoff = fibre glass reinforced plastics, kurz FRP). GfK besteht zum einen aus Fasern, nämlich Glasfasern, und zum anderen aus einer Kunststoff-Matrix, die die Glasfasern umgibt. Durch den Verbund von Glasfasern und der Kunststoff-Matrix wird GfK zu einem leichten und sehr robusten Werkstoff.
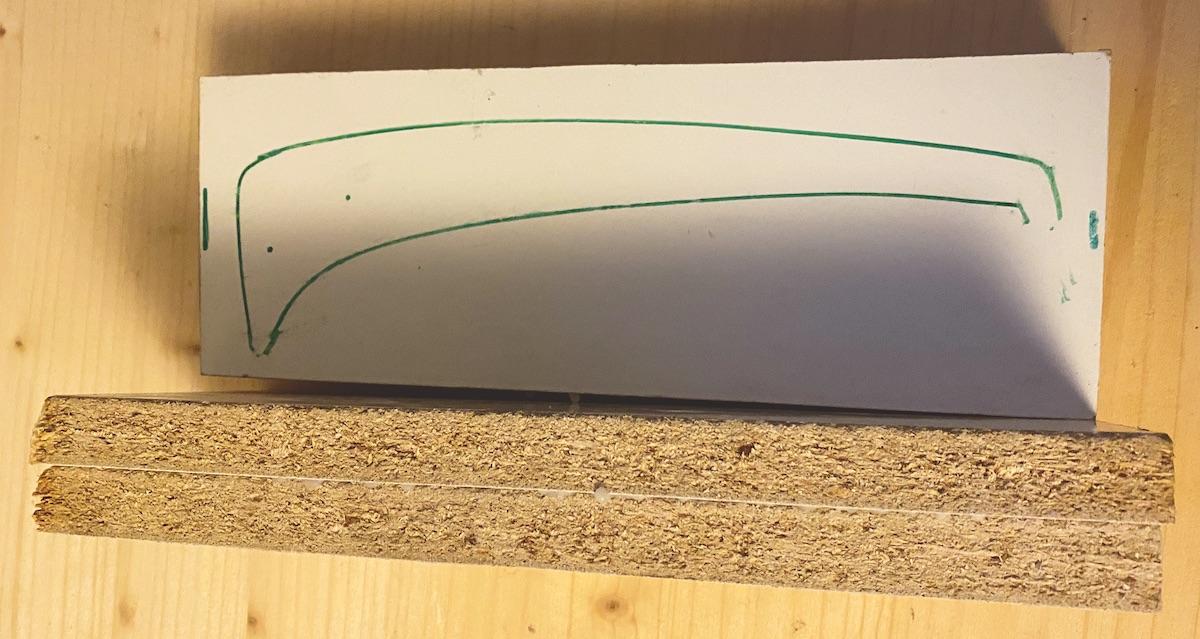
Für den Faserverbundwerkstoff GfK werden meist Duroplaste wie ungesättigtes Polyesterharz, Epoxidharz oder Vinylesterharz als Matrix verwendet. Im Modellbau hat sich heutzutage so gut wie ausschließlich Epoxidharz durchgesetzt. Epoxidharz wird üblicherweise in zwei Komponenten geliefert, die vom Anwender gebrauchsfertig zu mischen sind. Die sogenannte »A-Komponente« enthält meist das Epoxidharz, die »B-Komponente« den Härter, der in einem vorbestimmten Mischungsverhältnis dem Harz zuzugeben ist.
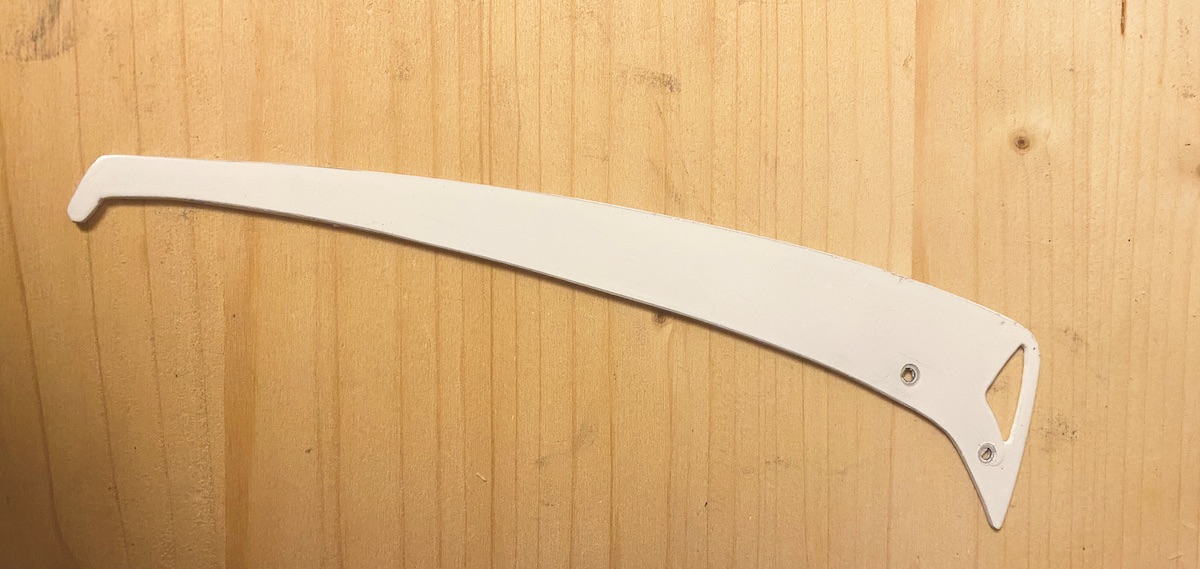
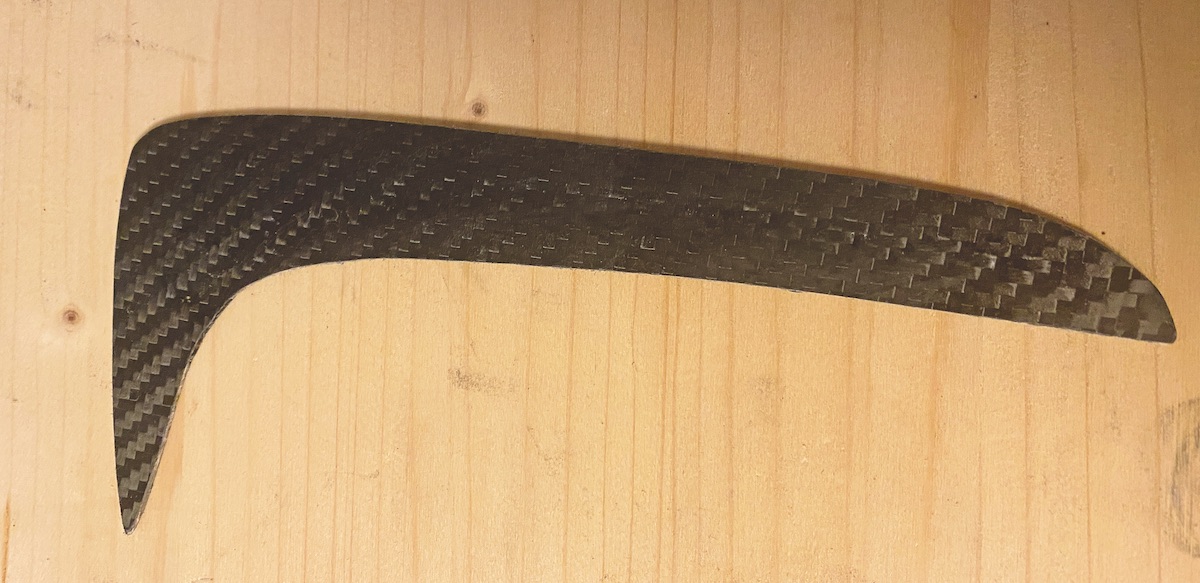
Die reine GfK-Verarbeitung im Modellhelibereich beschränkt sich heutzutage größtenteils nur noch auf die Fertigung von Hauben und Rümpfen. Alle weiteren Anwendungen werden eher durch die CfK-Technik ersetzt.
CfK (carbonfaserverstärkter Kunststoff) bezeichnet den Verbund von Kohlefasern und der erwähnten Kunststoff-Matrix. Carbonfaser, manchmal auch Kohlenstofffaser genannt, sind industriell gefertigte Fasern, die so veredelt werden, dass sie nahezu ausschließlich aus Kohlenstoff bestehen. Sie sind mikroskopisch klein und etwa um das Achtfache dünner als ein menschliches Haar.
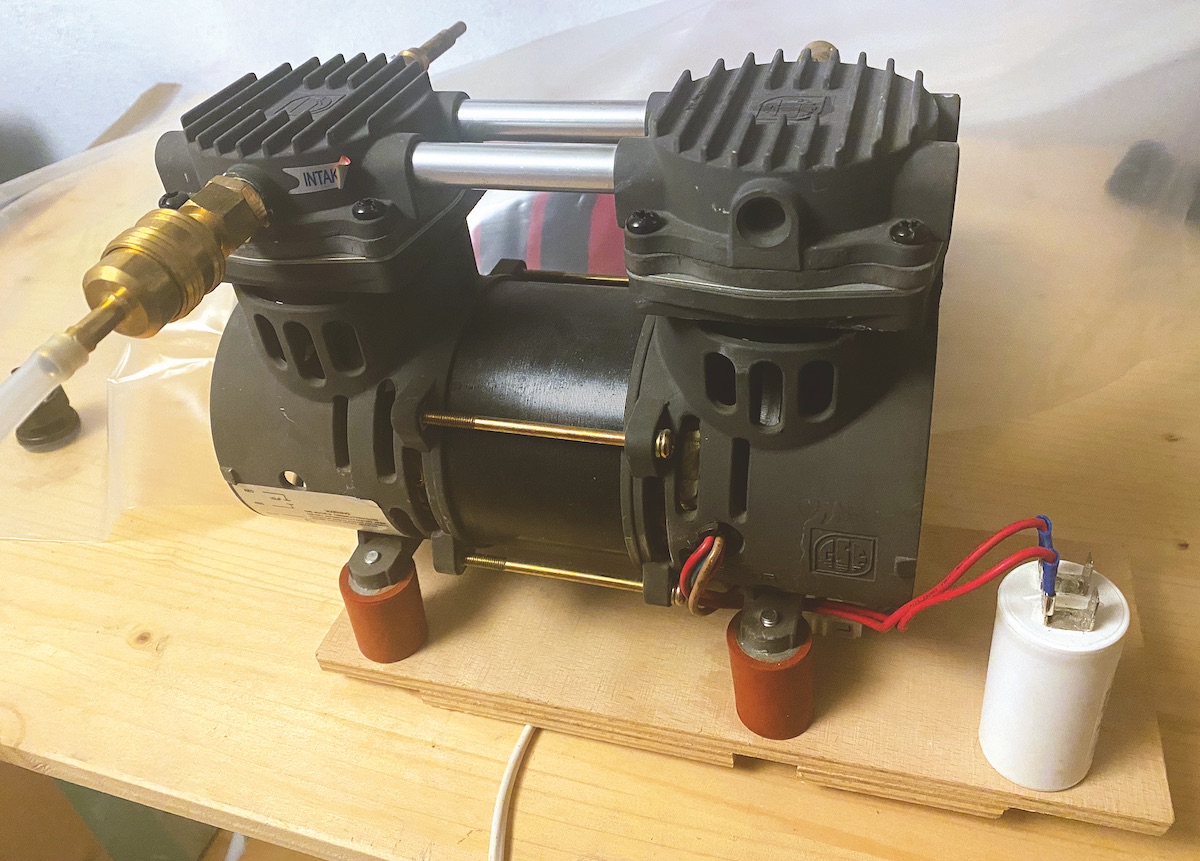
Besonders im RC-Heli-Bereich sind die Carbongewebe und Carbonfasern nicht mehr wegzudenken: Chassisplatten, Fahrwerke, Heckrohre, Heckabstützungen, Steuergestänge, Leitwerke und natürlich Haupt- sowie Heckrotorblätter.
Im Folgenden konzentriere ich mich daher schwerpunktmäßig auf die Verarbeitung von Carbonfasern.
Herstellung von Carbon-Seiten- und Höhenleitwerken
Ein Seitenleitwerk lässt sich ohne Schwierigkeiten selbst herstellen, unter der Voraussetzung, dass das Seitenleitwerk nur zum Schutz der Heckrotorblätter vor Bodenkontakt dient. Sollte das Leitwerk auch noch Kugellager tragen, ist von der Herstellung im Bastelkeller abzuraten. In diesen Fällen müssen die Bohrungen für die Schrauben und die Passung für die Lager professionell hergestellt werden.
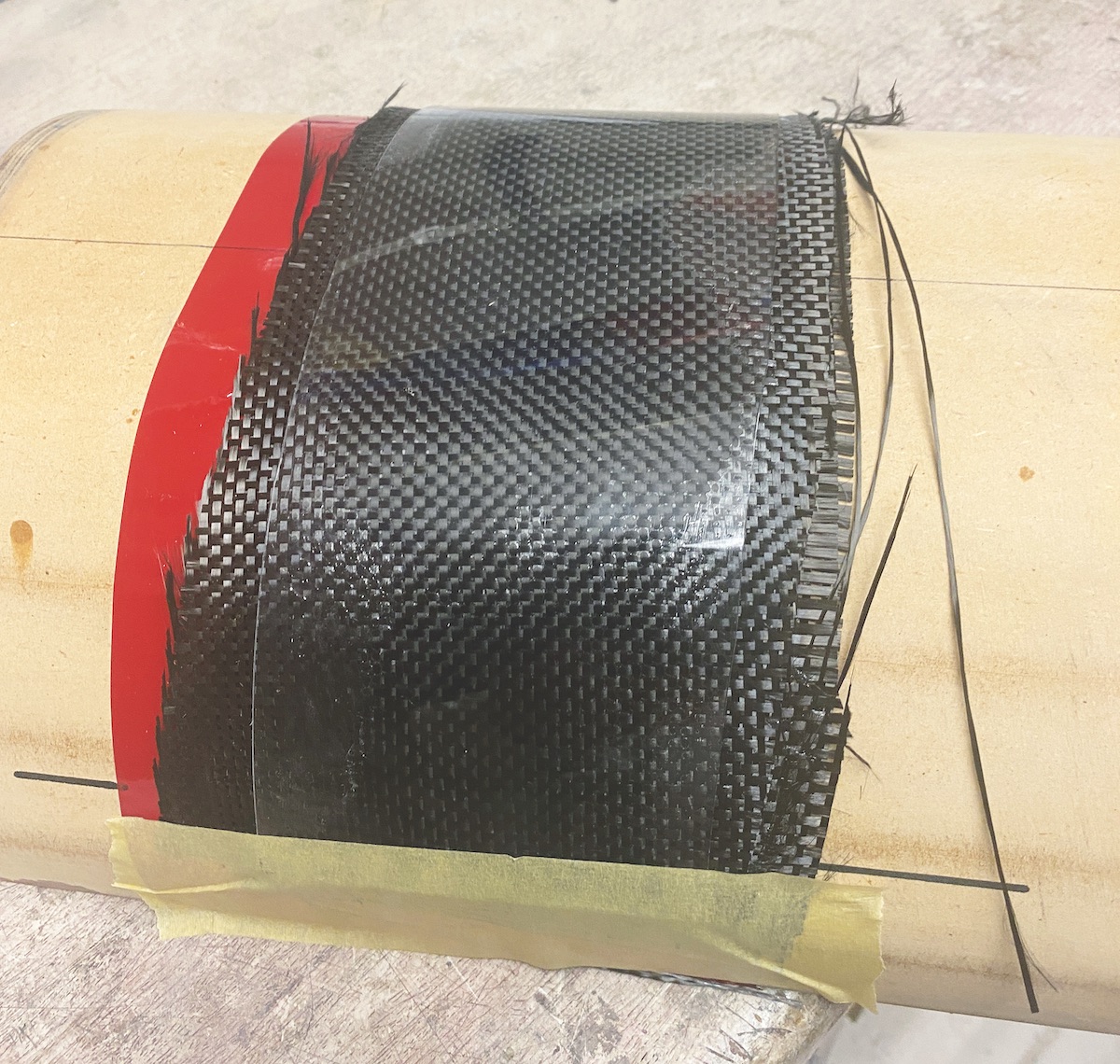
Zur Herstellung eines Carbon-Seitenleitwerks reichen für die Deckschichten zwei Lagen 165-g-Carbongewebe in Leinen- oder Köperbindung und zehn Lagen unidirektionales 150-g-Gewebe von R&G (www.r-g.de). Dieses unidirektionale Gewebe hat den Vorteil, dass die Filamente durch ein sehr dünnes Haftfadengitter aus Polyester zusammengehalten werden, sodass beliebige Zuschnitte ohne Ausfransen möglich sind. Somit bleiben die Faser nach einem Zuschnitt exakt parallel angeordnet, was bei einem Gewebeband nicht der Fall ist.
So ein hergestelltes, mit Schraubzwingen verpresstes Leitwerk ist unwahrscheinlich stabil, hat eine Dicke von ca. 1,8–2 Millimeter und ist sehr leicht (Carbon-Optik ca. 8 Gramm, in Weiß ca. 10 Gramm). Für ein Carbon-Höhenleitwerk reichen …
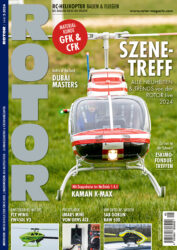
⇢ Den vollständigen Bericht lesen Sie in Ausgabe 5/2024. Ausgabe bestellen.