Thomas Gorba sprach JetPower-Redakteur Winfried Ohlgart auf der JetPower-Messe 2010 an und berichtete von seinem Projekt, ein Bell Jet Ranger-Cockpit im Maßstab 1 : 1 als Flugsimulator zu bauen. Gleichzeitig stellte er in Aussicht, diesen Simulator nach seiner Fertigstellung auf der JetPower auszustellen, um interessierten Besuchern die Möglichkeit zu einem Hubschrauber-»Flug« zu geben.
Auf der JetPower 2011 trafen sich beide wieder. Es erfolgte die Einladung nach Sinzig, wo in der Werkstatt das Objekt der Begierde bestaunt werden konnte – und das hat unserem Redakteur schier die Sprache verschlagen. Natürlich ergaben sich viele Fragen, deren Antworten unseren Lesern nicht vorenthalten werden sollen.
Winfried Ohlgart: Wie kommt man auf die Idee, ein Hubschraubercockpit im Maßstab 1 : 1 als Simulator zu bauen?
Thomas Gorba: Da ich Diabetiker (Typ1) bin, ist es mir leider nicht vergönnt, die Pilotenlizenz zu erwerben. Also habe ich mir gesagt, dann hole ich mir eben mein Fluggerät nach Hause – und da ich Hubschrauberfan bin, wurde es schlussendlich dieser Nachbau des Bell 206 Jet Ranger.
WO: Wann ging das Ganze los?
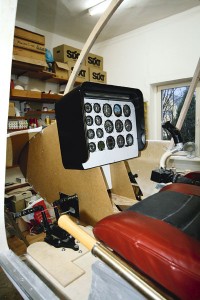
Sicht auf das Main Panel. Die Fluginstrumente sind maßstabsgetreu und servogesteuert.
TG: Angefangen hat es mit dem Microsoft Flugsimulator 2005, der allerdings eine ziemliche (Hubschrauber-)Katastrophe war. Die Flugeigenschaften des Jet Ranger in dieser Software waren in etwa die eines am Propeller hängenden Flugzeugs. Später wurde das dann immer besser und realistischer. Der FSX ist schon ein fantastisches Flug- und Szenerie-Erlebnis! Man kann mittlerweile auch auf Lastwagen und Yachten landen, darüber hinaus auch Lasten aufnehmen und absetzen, was den Kick um einiges erhöht. Bis 2008 »flog« ich mit einem modifizierten Joystick mit angekoppeltem Schubregler, der einen integrierten Wippschalter zur Steuerung des Heckrotors besaß. So baute ich mir meine erste Hubschrauber-taugliche Steuereinheit. Den Wippschalter verband ich via Fahrradbremszügen mit meinen selbstgebauten Fußpedalen. Zusätzlich vervollständigte ich nach und nach meine Fluginstrumente, die als servogesteuerte Scale-Nachbauten von einer niederländischen Firma zu haben waren. So bestand mein erstes Main Panel aus sechs der begehrten Fluginstrumente, umrandet von einem Gehäuse aus Pappe. Dieses Setup flog ich, bis der Joystick 2008 seinen Geist aufgab, und da habe ich dann beschlossen, mit dem Bau des Simulators zu beginnen. Genauer gesagt, lud ich mir ein Foto eines Jet Ranger Main Panels aus dem Internet und baute es frei Hand nach, da ich damals noch keine Kontakte hatte, wo ich mir Maße und Details hätte besorgen können. Nachdem ich fertig war, schloss ich mich einem Hubschrauber-Simulator-Forum an (www.hovercontrol.com) und begann, meine Arbeit in diesem Forum zu dokumentieren. Seitdem ist mein Projekt so eine Art Doku-Soap geworden, die reges Interesse findet, da ich den größten Teil meines Projekts mit einfachstem Equipment realisiert habe.
WO: Was man hier sieht, ist ja nicht nur der Bau einer Cockpitsektion, sondern ich sehe auch Originalteile. Das fängt beim Steuerknüppelgriff an, geht über ein paar Schalter und hört beim Pitchhebel und den Fußpedalen auf. Wie kommt man an solche Teile ran
TG: Da klingt schon fast wie eine klassische Weihnachtsgeschichte. Zu Beginn meines Projekts verschaffte ich mir Maße und andere Informationen meist durch Abtelefonieren von Unternehmen, die mit Hubschraubern oder Hubschrauberteilen zu tun hatten. Irgendwann telefonierte ich dann mit einem Avionik-Händler aus Andernach, der meine Motivation aus persönlichen Gründen nachvollziehen konnte und gerade das Wrack eines Twin Rangers im Hangar hatte. Er lud mich zu einem persönlichen Treffen ein und schenkte mir einfach so den Pitchhebel, die zwei Fußpedale und zwei Sitze! Dafür bin ich noch heute sehr dankbar, da diese Teile auch gebraucht und fluguntauglich noch richtig viel Geld kosten. Für die anderen Sachen muss man eben, wie die Modellbauer auch, weltweit recherchieren – so geschehen bei den genauen Cockpitmaßen, Informationen über die Einbauten und der Anordnung der Instrumente.
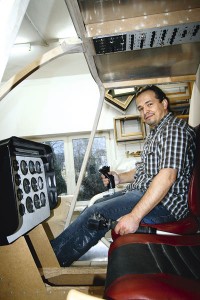
Erbauer Thomas Gorba in seinem Cockpit –
Großmodellbauer mit Leib und Seele. Er hat bereits Anfragen zu neuen Projekten.
WO: Ich kenne solche Projekte auch aus der Jetfliegerei; da geht das natürlich auch sehr schnell ins Geld, und deshalb wird so mancher Kostenpunkt auch geheim gehalten. Wenn ich diesen Aufbau so vor mir sehe, kommt natürlich die Frage auf, wie viele Arbeitsstunden und wie viel Geld da drin stecken?
TG: Zu den Kosten kann ich gar nicht so viel sagen, weil ich mir viele Materialien aus Resten zusammengesucht habe. Bei diesem Vorhaben kann man aber auch viel selber machen, wenn man handwerklich geschickt ist. Die Arbeitsstunden habe ich nie aufgeschrieben, aber anhand meiner Bildordner kann ich sagen, dass ungefähr 800 Stunden für Planung, Recherche und Dokumentation aufgewendet wurden und dass im Cockpit bis jetzt 1.500 bis 1.800 Arbeitsstunden stecken.
WO: Als ich bei Ihnen ins Atelier gekommen bin, habe ich eine Fräsmaschine, eine Drehbank und lauter hochwertige Werkzeuge erwartet. Was ich aber sehe, sind eine Tischkreissäge und eine Ständerbohrmaschine. Wo haben Sie die anderen Werkzeuge versteckt?
TG: Ich habe nur die Werkzeuge verwendet, die ich auch in meinem Atelier, in dem ich hochwertige Bilderrahmen fertige, nutze, und habe damit wirklich ganz rudimentär vorwärts kommen müssen. Deshalb ist vielleicht das eine oder andere Teil nicht absolut exakt geworden. Wenn es mal an den richtigen Werkzeugen fehlte, waren eben Hirn, Kreativität und handwerkliches Geschick gefordert. Das ist ein weiterer Grund für das große Interesse an meiner Dokumentation im HoverControl-Forum. Ich habe einige kreative und innovative Lösungsansätze geliefert, die z. T. von anderen Cockpitbauern in ihre Projekte übernommen wurden. Die Spezialbauteile wie z. B. die Mischerplatte und der Cyclic Support sind dann für mich von Leuten gemacht worden, die entsprechende Maschinen haben. Ich musste natürlich die Zeichnungen mit den Maßen anfertigen.
WO: Dabei sind Sie im Internet auch auf ein Material gestoßen, das sich für die Bugsektion hervorragend geeignet hat – und wie Sie eben erwähnten, durchaus als kreative Lösung bezeichnet werden kann.
TG: Ja genau, es heißt Holzmaché. Man kann das Zeug fertig kaufen – es lässt sich aus Sägemehl, Wasser, Leim und Tapetenkleister aber ganz einfach auch selbst herstellen; das Rezept gibt’s im Internet. Der Hauptgrund für diese Alternative zu GfK war, dass mein Sohn und ich möglichst wenig Emissionen ausgesetzt werden sollten.
WO: Diese Masse haben Sie dann auf ein Gerüst aus Kaninchendraht aufgetragen und weiterverarbeitet. Wie lässt sich Holzmaché schleifen, und verläuft es nicht beim Auftragen?
TG: Das Gerüst besteht im Wesentlichen aus Aluminiumprofilen, die das Tragegerüst bilden. Daran habe ich den verzinkten Kaninchendraht befestigt. Damit das Holzmaché nicht durch die Maschen fällt, wurde die gesamte Haube von der Innenseite mit Pappmaché beklebt. Zum Schluss habe ich dann das Holzmaché flächig aufgetragen. Wenn die Mischung richtig ist, hat die Masse die Konsistenz von Erdnussbutter, und die klebt, wie jeder weiß, ja überall. Genauso verhält sich auch Holzmaché. Es verläuft nicht, und man kann damit sogar über Kopf arbeiten. Sie schrumpft auch nicht, braucht allerdings lange zum Trocknen. Dafür kann man aber auch locker Schichtdicken von bis zu 2 cm auftragen. Nach dem Trocknen lässt sich Holzmaché wie Holz gut mit der Raspel, dem Schwingschleifer und Schleifpapier bearbeiten.
WO: Was wir hier sehen, ist die Hardware. Wie sieht es mit der Software aus, denn irgendwann ist das Cockpit ja fertig; wie geht es dann weiter?
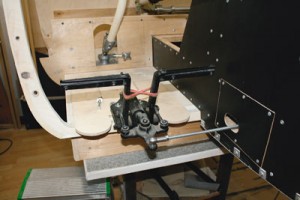
Die Pedale zur Steuerung des Heckrotors, ebenfalls Originalteile. Die Steuerstangen führen direkt zum Bewegungsmelder in der Mittelkonsole. Hierbei wurde ein Hall-Effekt-Sensor eingesetzt.
TG: Der nächste Schritt ist die Installation der Elektronik. Das Ganze läuft über Controller, die die Hardware mit dem Microsoft Flight Simulator verbinden und die Steuerimpulse an die Simulationssoftware weiterleiten. Allerdings muss ich vorher noch eine riesige Herausforderung meistern: die Verlinkung der Mischerplatte mit den Potis, die die Impulse an den Controller weiterleiten. Dabei muss ich die Bewegungen von X- und Y-Achse noch separieren. Ich bin nicht der große Elektronikfachmann, aber da dieses Projekt in der Zwischenzeit schon von vielen guten Geistern begleitet wird, wurde mir bereits von vielen Seiten Hilfe angeboten.
WO: Wie bekommen Sie dann den fertigen Simulator hier aus dem Raum heraus?
TG: Der Simulator ist so konstruiert, dass er in mehrere leicht zu transportierende Teile zerlegt werden kann. Genauer gesagt so klein, dass er durch die klassische Dachbodenluke passt.
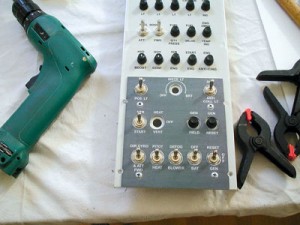
Das Overhead Panel wurde ebenfalls anhand von Fotos des Originals reproduziert.
WO: Wenn es dann soweit ist, bin ich natürlich wieder hier, denn das wird sicher eine interessant Sache werden, wobei ich vermute, dass noch etliche Kilometer Kabel zu verlegen sind.
TG: Das schöne beim Jet Ranger ist, dass es ein simpler Hubschrauber ist, bei dem der Aufwand nicht so sehr hoch sein wird. Aber wie ich schon sagte, bin ich kein Elektroniker, und deshalb steht mir schon jetzt der Schweiß auf der Stirn, wenn ich nur daran denke. Aber wie heißt es so schön: no pain, no gain!
WO: Das ist bei uns in der Modellfliegerei oft nicht anders. Man fängt ein Projekt an, und mitten drin denkt man: Oh Gott, was hast du dir da nur angetan! Wir sollten noch erwähnen, dass der Simulator auf der JetPower 2012 zum zehnjährigen Jubiläum der Messe zu sehen und am Stand des Modellsport Verlags zu »fliegen« sein wird!
TG: Ich freue mich schon darauf, mein Projekt auf dieser großen internationalen Messe vorstellen zu können. Bis dahin ist noch viel Arbeit und auch Unterstützung nötig. Ich brauche dafür unter anderem einen guten und starken Beamer, und ich freue mich, dass mir die neuseeländische Firma Ruscool electronics (www.ruscool.co.nz) ein bestücktes Avionik-Panel zur Verfügung stellen wird. Dieses kreative und äußerst engagierte Familienunternehmen fertig Simulationsinstrumente von bester Qualität und hat sich seit dem ersten Kontakt ganz fantastisch um mich gekümmert, damit zur JetPower auch alles da sitzt, wo es hingehört. Wir arbeiten gerade an der Umsetzung.
WO: Ich bin mir sicher, dass sich nach dieser Veröffentlichung der eine oder andere Sponsor bei Ihnen melden wird. Ich werde dann im Sommer wieder vorbeikommen, um mich über die Fortschritte zu informieren. Es war jedenfalls eine tolle Erfahrung, hier bei Ihnen sein zu dürfen, und ich wünsche Ihnen für die weitere Fortführung des Projekts viel Erfolg!
Das Interview führte Winfried Ohlgart ,
Bericht aus MFI, Ausgabe 8/2012